ITRI has developed an innovative robot joint module, the Detachable Robot Joint System, for the rapid assembly of various robots with different configurations, including different numbers of joints and various payloads. This innovative robot joint module utilizes EtherCat for communications among peripherals for integration and coordination such as various sensors, drive controllers, encoders, motors, and brakes. Its compact design helps achieve the world’s highest torque-to-volume ratio. Instead of the time-consuming substitution of robot arm joints due to repair and maintenance, only five minutes is adequate for joint replacement via the detachable mechanism designed in ITRI’s robot joint. This innovative robot joint with a rapid detachable mechanism will enable new thinking about use cases, and it can be applied to diverse industries such as machinery, manufacturing, medicine, and even services.
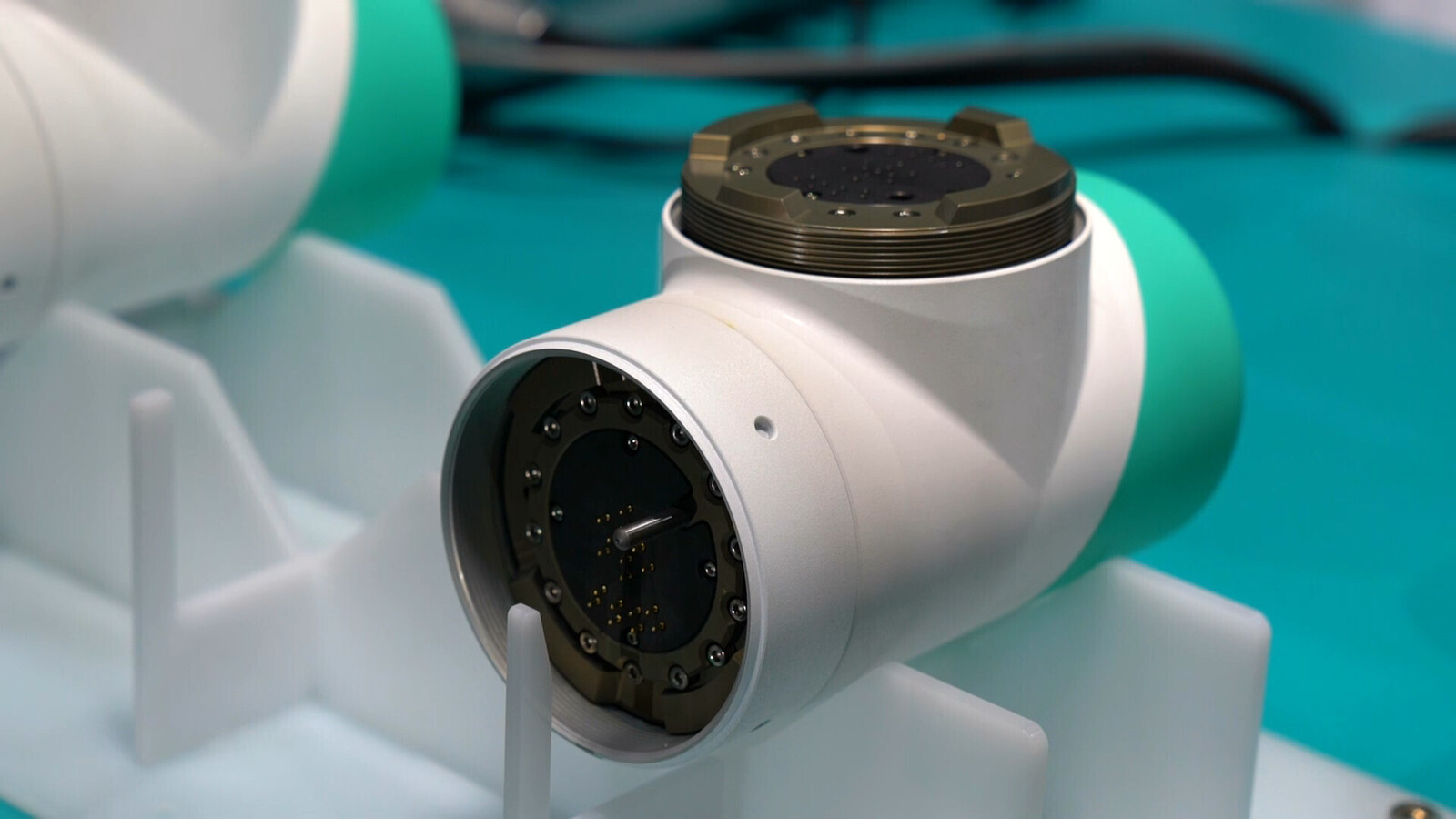
Rapid assembly of various robots is feasible with different configurations, including different numbers of joints and payloads.
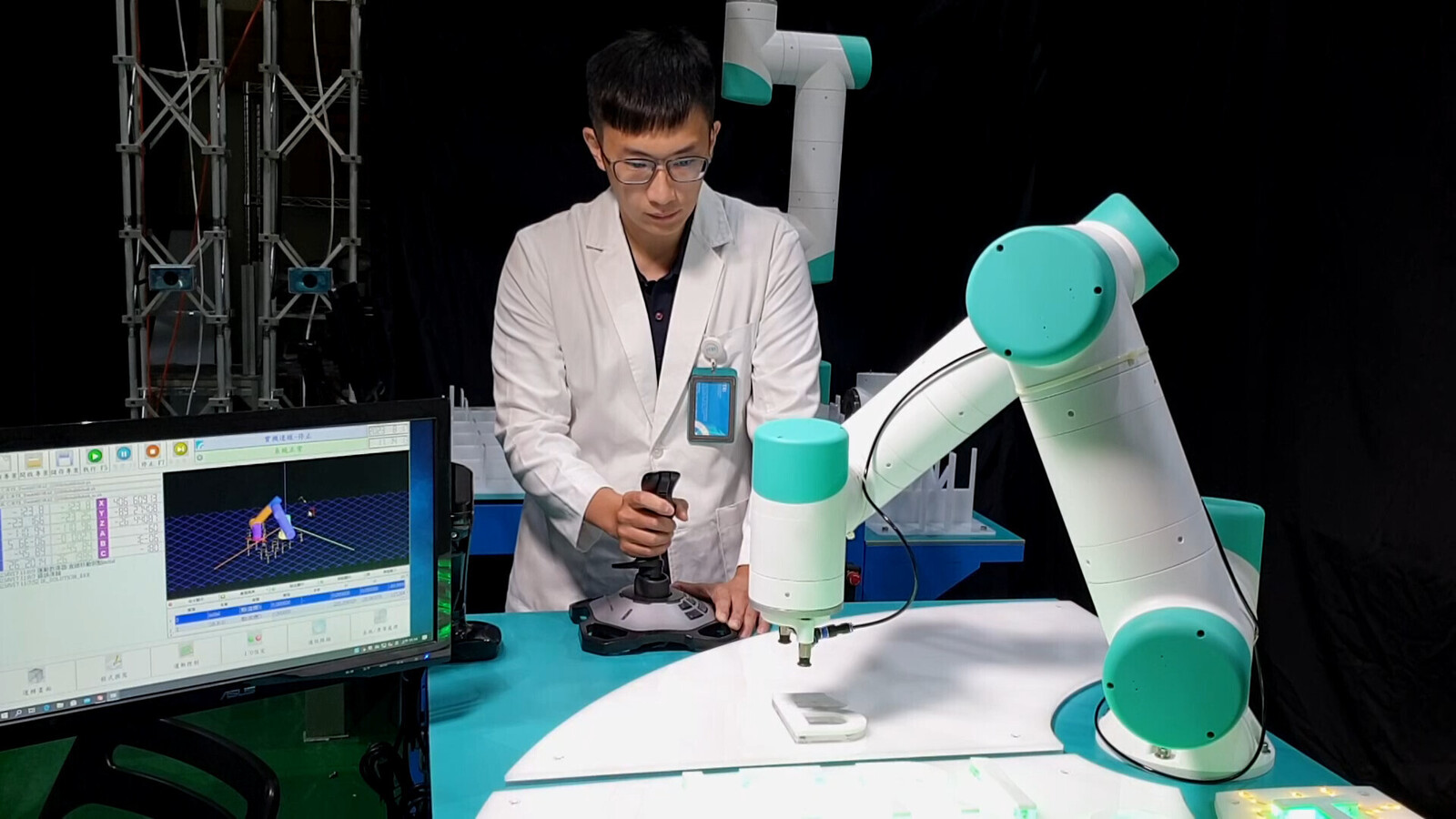
The system utilizes EtherCat for communications among peripherals for integration and coordination such as sensors, drive controller, encoder, motor, and brake.